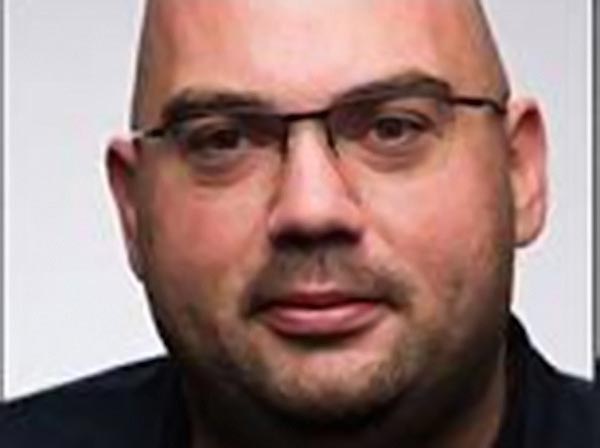
Click to learn more about author Alex Fielding.
In a recent survey, 79 percent of content management professionals admitted that more than a quarter of their organizations’ total records are still on paper documents. The same research also showed that 93 percent of respondents believe extracting smart data from paper records would revolutionize the value of that data for the business, with 70 percent saying the way to achieve this is with digitized records.
It’s not much of a leap to imagine similar problems 40 years ago, when the phrase ‘paperless office’ was just coming into common use. Decades later, our collective reliance on paper remains a source of frustration and inefficiency. As the research revealed, close to one-third of the survey respondents said it is difficult to access data from their paper records. Sixty percent say that these records slow down business processes while 93 percent agree that if all their paper records were lost, it would negatively impact their organization.
Furthermore, almost every content management professional surveyed at the event agreed that the ability to easily extract data from paper records would add value to their businesses. When specifically asked if digitizing would help, seventy percent said “yes”.
Thankfully, times are rapidly changing, and the arrival of digitization solutions that blend advanced robotics with artificial intelligence are enabling organizations to not only address the inefficiency of manual paper processing, but to extract new value from the data they create.
A prominent approach to the digitization challenge has seen it build and patent robots that can sort and scan paper and make the resulting data available for use. The technology automates 80 percent of the conversion process, which includes paper handling, fastener removing, and digital imaging. Specifically, robots are more efficient at removing staples and other fasteners, which minimizes risk of paper jams and tears. In contrast, manual cataloguing and indexing is error-prone.
As a result, this kind of technology can process an entire banker box within one to two hours; it would take a human about four to six hours to digitize the same content. When implemented at scale, this equates to processing thousands of boxes per day.
Using robots to digitize paper is also inherently more secure. Robots do 90 percent of the paper handling and 90 percent of the indexing, meaning organizations don’t need to worry about the wrong people reading the most sensitive documents.
The Real Thing: How Coca-Cola Bottlers’ Sales and Services Digitized its Supply Chain
Real-world examples illustrate the impact. For example, optimizing the supply chain through digitization can improve both efficiency and competitiveness, compared to organizations that rely on traditional methods of administering increasingly complex and dynamic supply chains that can leave them overwhelmed.
In particular, supply chain operations that rely heavily on paper and physical records for management face financial consequences when their systems fail to keep pace with fast-changing circumstances and demands.
The Coca-Cola Company (TCCC) and its bottlers, Coca-Cola Bottlers’ Sales and Services (CCBSS), are multinational organizations with complex logistics made up of suppliers and channels.
They have a unique approach to scaling their business by franchising the manufacturing, packaging, and logistics to the CCBSS “bottlers” that fulfil the orders fulfilment of Coca-Cola customers. While TCCC outsources all of its manufacturing and logistics management of its products to CCBSS, it owns the contracts with customers like Costco, Walmart, Kroger, etc.
The existing process required CCBSS to provide evidence of the fulfilment of goods and services each month. This is achieved via a proof of delivery (PoD) ticket between the deliverers and receivers. The burden of proof falls to the bottlers – if the document isn’t provided, the customer won’t pay the bill.
The pre-digital procedure was to photocopy the PoD at the bottlers’ office and then FedEx the original to a supply chain management company. However, because CCBSS contracted seven different companies to support the ecosystem that each single document was sifted through, it was suffering from an overly complex and inefficient system. The result was a process that was losing millions of these documents a year, with a significant impact on revenue.
Recently, CCBSS decided to digitize parts of its operation including supply chain management in order to maximize accuracy and efficiency. Through digitization, CCBSS estimates that it will soon save millions of dollars by consolidating vendors through document lifecycle management. The document management, image storage, indexing, and physical storage and shredding suppliers have been replaced with the Ripcord solution and turned what was once a bird’s nest of process outsourcing into a streamlined system with advanced technology that can index tens of millions of documents and do it with far greater levels of quality, accuracy, and speed.