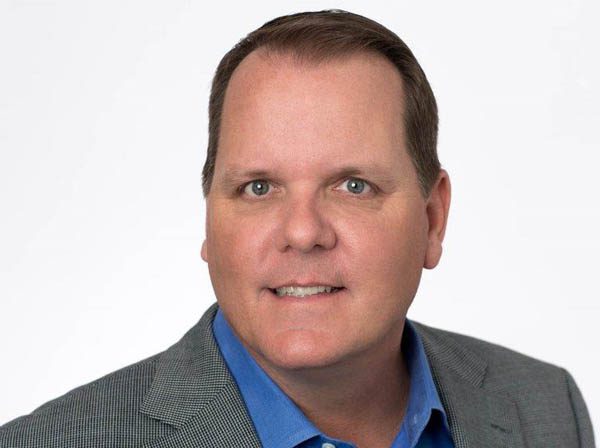
Click to learn more about author Keith Higgins.
Over 60% of manufacturers are planning to increase their investments in smart factory initiatives over the next few years. That ratio will undoubtedly increase as existing digital transformation projects continue to scale up post-pandemic and new cutting-edge enterprise technology solutions emerge over the next few years.
When looking at the different functions across an industrial enterprise today, including product and machine design, production engineering, plant operations, and supply chain, you will find many legacy software applications where data is locked up. For manufacturers, data silos typically build up in systems used for day-to-day planning and operations, including enterprise resource planning (ERP), electronic manufacturing services (EMS), manufacturing execution systems (MES), manufacturing operations management (MOM), or other software systems and tools.
When these various enterprise systems are not integrated across an organization, manufacturers may miss critical insights that could improve factory operations. As Sujeet Chand, our company’s CTO, highlighted at our recent Automation Fair at Home event, “It is critical that organizations tie these siloed functions together digitally to get operational value from their digital transformation initiatives.”
Digital Thread: Tying Enterprises Together
A digital enterprise connects assets, systems, and processes across an organization. However, optimizing digital transformation initiatives requires a way to visualize how those components work together as data flows through an industrial ecosystem. The digital thread offers a detailed, virtual perspective of information flows – production performance data (e.g., speed, downtime), product specification data (e.g., quality parameters, system rejects), supply chain data (e.g., inventory levels, late deliveries, quality), etc. Basically, a digital thread is the trail of information collected throughout the lifecycle of a product, asset, system, or process. This digital record provides the entire value chain with universal access to unified digital data captured during design, virtual simulation, and physical operations. Executives and leaders can leverage the digital thread to help to evaluate and improve value streams in real time.
Digital mirroring of your plant and information flow can provide critical insights for better daily management. Here are three different ways digital thread improves business value:
1. Accelerate Innovation
Success in manufacturing has always been tied to capacity to innovate quickly. Digital thread enables accelerated innovation through real-time collaboration. Manufacturers no longer need to email design files across their organization, accepting that there will inevitably be version control issues. Machine builder engineers, who are designing the machine, and field engineers on site establish a single source of truth by exchanging information in real time. Organizations can remove dependencies by bringing every stakeholder together in real time from the start. They can kick off product design, machine design, and production engineering simultaneously to reduce timelines and evaluate design manufacturability.
2. Optimize Operations
The key to optimizing operations is connecting the plant to the digital content created by other business functions. Digital thread can be used to commission new production lines virtually – enabling manufacturers to decrease time to market and protect investments. Rather than waiting to commission manufacturing lines until the machinery is bolted to the plant floor, manufacturers can ensure that operations will run smoothly by validating manufacturing processes and debugging programmable logic controller (PLC) code via a digital twin.
3. Maximize Workforce Productivity
Workforce productivity is top-of-mind for many organizations, with 58% of the workforce approaching retirement and processes that are becoming increasingly complex. With digital thread, organizations can empower their workforce to reach their potential with high-fidelity training and on-the-job instruction. With access to hands-free, step-by-step directions, new personnel are equipped to deliver a first-time fix their first day on the production floor. From veterans to new hires, digital thread connects business systems together to enable the creation of a historical record of all trainings and on-the-job instructions needed to keep production running smoothly. Virtual reality and augmented reality can shorten training time by as much as 75% by enabling low-risk, high-fidelity environment training and real-time equipment instruction for new or retrained employees.
For example, our company helped a global manufacturer implement a digital thread alongside MES at most of its 20 manufacturing locations, resulting in a 50% lead time reduction to customers, a 50% reduction in defective parts, and a 4% improvement in productivity. This performance boost increased both customer satisfaction and market share.
The pace of innovation is faster than ever. To stay ahead of the competition, organizations must maximize workforce productivity and optimize operations by delivering information to the appropriate person or system at the right time. Manufacturers seeking to realize their full digital potential and reap the highest ROI when it comes to digital transformation must futureproof their digitization investments and rethink the way they manage operations by leveraging digital thread.