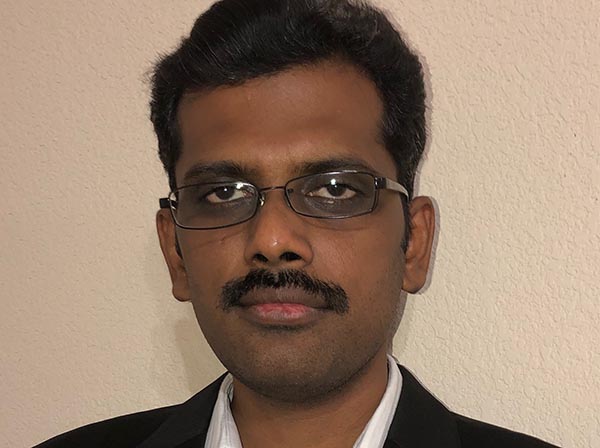
Click here to learn more about author Mahendraprabu Sundarraj.
The benefits of digital transformation – Competitive edge, deduction in operational expenses, and improved product quality – are indisputable. Many manufacturing companies have started transforming their manufacturing operations or at least plan to start soon.
Digital transformation is never a one-time exercise, but a continuous improvement program. Lack of strategy, architecture, and tools not only make the digital transformation program a failure, but also sub-optimize the existing production efficiency. This article focuses on the top four challenges a manufacturing organization would face in planning and executing digital transformation program.
The Gap Between IT and OT
Operational Technology (OT) that comprises of cyber-physical systems and the Industrial Internet is not technically too far from the Enterprise IT and Infrastructure Departments. However, the operations team owns the OT, and they either create the edge devices or work with an industrial equipment vendor company to set up the edge devices at the production site. The operations team’s focus is more on running the efficient operation with the help of edge monitoring devices and very less on the overall enterprise-level digital transformation goals.
The convergence of the IT team and the Operations Technology Team is critical to digital transformation success on a production floor. IT and OT collaboration must start from the design phase, not just from post-implementation phase. Early collaboration would help in getting aligned on security standards, system latency requirements, communication protocols between edge devices and enterprise cloud, standard data formats, monitoring goals, and change management process. This alignment is essential to build useful digital applications efficiently and cost-effectively. Lack of alignment would throw surprises that can discourage organizations either to limit or to stop their digital transformation program.
Lack of Analytics Strategy
Given the cheap cloud infrastructure, improved network bandwidth, and processor speeds, organizations can kick start the digital transformation very quickly and can see very significant value return in the initial phase of digital transformation itself. However, In the initial phase, organizations are expected to achieve only a descriptive or diagnostic level of analytics maturity. Though this initial maturity level gives a significant value over the previous state, initial success would not be sustainable unless there is a strategy in place to advance analytics maturity level to predictive or prescriptive. Lack of strategy will limit the organizations to change, and very soon, the benefits of the initial success will become irrelevant. Besides, if there is no strategy, it is hard to estimate how much an organization would spend over a few years for a digital transformation program; cloud costs can very quickly pile up and derail the digital transformation.
Latency
Manufacturing organization IT infrastructure cannot completely operate in the cloud alone due to cost and security. Hence hybrid cloud (a combination of on-premise and cloud) has been widely accepted as the suitable IT infra-architecture for smart factories. However, the hybrid cloud can become a challenge to reach real-time operational analytics goals.
Executive Sponsorship
As mentioned above, digital transformation is a continuous improvement exercise. Challenges and the increase in expenditure in this never-ending journey can easily discourage executive team’s commitment. As per Deloitte’s report in 2017, IT spend of manufacturing companies is approximately 1.95% of their total revenue. This estimation is based on the typical IT infrastructure a manufacturing company would have had before Industry 4.0. Digital transformation programs can increase this estimated spend significantly. Executive leadership must stay convinced about the value of digital transformation and stay committed with realistic expectations about the expenditure.
Organizational structure challenges, lack of internal expertise and agreement to execute, and failure to identify the high-value operational use cases are additional challenges a manufacturing organization should be concerned about. Since these challenges are faced only during the initial planning phase of digital transformation, this article focused on challenges that are faced in multiple stages and have a profound impact on realizing value out of digital transformation programs.