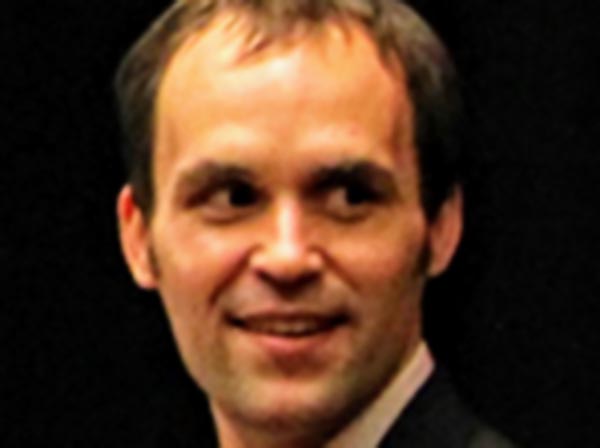
Click to learn more about author Jeff Kinard.
Every organization strives to deliver high-quality data to support and inform better decisions. Ensuring robust data is essential as businesses seek to optimize operational efficiency. Recent research found that 95 percent of organizations see negative impacts resulting from poor Data Quality.
When it comes to asset-intensive industries, Data Quality is paramount and not just to drive productivity gains. The quality of data has a direct relationship with the safety of the working environment. Bad data results in less than optimal decisions around repairs, maintenance, and even downtime. This can range from something relatively minor, such as a wrench failing on a job, to a more significant disruption, such as a gas pipeline not being maintained and failing. The impact of these problems could lead to an unplanned outage, incurring substantial financial losses combined with a safety incident. In some situations, this could create a potentially catastrophic event resulting in loss of life.
If an organization relies on a reactive maintenance approach, the repair activity is triggered by the equipment failure, which means that the machinery operated less optimally for a period of time. This drives up the number of safety incidents and maintenance costs, along with unplanned downtime.
So, Data Quality is not optional; it is mission-critical for enterprise asset management organizations. Most asset-intensive businesses allocate a significant portion of revenue towards maintenance programs. As a result, they need to rely on high-quality data that they trust to reduce the risks of safety incidents occurring, in addition to the operational benefits.
Predictive maintenance techniques help optimize the management of assets by:
1. Collecting, analyzing, and acting on data about machines
2. Understanding how industrial processes work
3. Predicting when equipment is likely to fail and taking action before a problem occurs
This approach minimizes costly downtime due to unexpected malfunctions, helps save money on maintenance costs, and critically improves workers’ safety. As a result, enterprise maintenance continues to move towards preventive and predictive strategies, as planned maintenance reduces the risks.
However, the transition from reactive to predictive maintenance is dependent on the quality of the data used to inform better decisions. As a result, this can reduce the risk of keeping end-of-life equipment in operation. Poor data is often the catalyst behind many outages, equipment failures, and malfunctions, which in turn drives up safety incidents. With the organizational safety benefits and continuous improvement in processes that quality data enables, every asset-intensive organization needs to strive for ways to achieve consistent, accurate information about safety-critical assets.