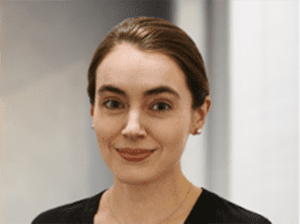
Industrial environments are rich data sources, from equipment pressure and temperature readings to real-time inventory levels. This ocean of data provides organizations with valuable insights when (and if) effectively harnessed. By transforming raw data generated across the floor 24/7 into actionable intelligence, industrial plants are equipped with data-informed insights necessary to create operational strategies that reduce costs, improve safety, and enhance their competitive edge.
Beyond simply a collection of ones and zeros in a server or mere record-keeping for these industries, industrial data management has developed into a strategy to visualize present performance that helps shape the future. With a clearer picture of operations, plants identify a path forward for improved reliability, availability, and performance. As a result, industrial organizations continue to build their data management foundation, recognizing that future success hinges on their ability to manage and scale data-informed operations, strategy, and decision-making.
Origins of Industrial Data Management
Data serves as the foundation for creating information and knowledge. Overall, data is the building block for future value, but it needs to be transformed into information. Information provides context for understanding; however, it requires focus to avoid overload. And knowledge is the application of information based on experience. Throughout history, people have developed methods and technologies to facilitate this flow of data to information to knowledge – and industrial organizations are no different.
One flow of data to information to knowledge for plants and facilities has centered around connecting physical measurements to operators and engineers with the necessary mechanical, electrical, and chemical expertise. And this is not anything new. Industrial environments have long been a rich source of time-series data. Unlike transactional data, time-series data consists of a sequence of data points collected at regular intervals. For example, the temperature readings of a boiler over time represent time-series data. This information allows equipment operators and engineers to monitor equipment and process statuses and make informed decisions about operation and maintenance.
Though this process from data to knowledge is not new for industrial plants, it has changed over the years. Before the third industrial revolution in the mid-20th century, data collection in industrial settings relied on manual processes. Operators would conduct rounds at predetermined intervals. They recorded data points using various tools and methods, from analog gauges to manual sampling and from paper logs to punch cards. Industrial organizations used these methods to generate, collect, and analyze data for day-to-day operations. In fact, the industry recognized the importance of instrumentation (that generate and manage industrial data) so much that Richard Rimbach and other industrial experts formed the Instrument Society of America (now known as the International Society of Automation) in 1945.
However, these early methods of data collection had limitations. The need to schedule manual collection rounds hampered data accessibility. Physical space requirement for paper records constrained storage capacity. And time and resources limited industrial organizations’ processing capabilities. As a result, the industrial data management process of the past was far from comprehensive or efficient enough to keep up with the world’s evolving needs and demands.
Industrial Automation and Data Management
Industrial automation evolved significantly in the mid-20th century, leading to the Third Industrial Revolution. This era saw the introduction of Programmable Logic Controllers (PLCs) and the widespread adoption of computers in industrial settings. The automation of sensors and advancements in control systems, including SCADAs (Supervisory Control and Data Acquisition), DCSs (Distributed Control Systems), and PLCs, enabled industrial environments to not only effectively control their equipment but also generate large amounts of data 24/7.
This explosion of available data was not limited to industrial organizations. The 1960s witnessed increased activity in data processing and technology overall. From the founding of the Association of Data Processing Service Organizations (ADAPSO) to the release of the BASIC programming language; from the development of the Unix operating system to the advancements in floppy disk data storage. All played a crucial role in creating data processing services and spearheading the computer software and services industry as we know it today. And in 1970, Edgar Codd introduced the relational database model, which stores and retrieves data using tables and relationships. Codd’s work serves as a foundation for the development of SQL (Structured Query Language) and relational database management systems (RDBMSs).
However, the nature of equipment data in industrial applications required a different approach than the RDBMS structure. Industrial organizations needed time-series databases capable of managing large amounts of high-resolution data across a plant or fleet. This need gave birth to the data historian. In the industrial environment, a data historian is a specialized data management system that collects real-time sensor data and archives it for future use. Unlike an RDBMS that uses tables and relationships, a historian associates data points with a timestamp and signal (or tag).
With the development of data historians and time-series databases, data historians became increasingly used in industrial organizations during the late 20th century and early 21st century. However, there was still room for growth with data historians related to improved visualizations, access, and insights.
Continued Developments in Data Management
Today, the industrial sector, like many others, is at an inflection point in data management. As organizations and individuals continue integrating technology and real-time data insights into daily tasks, solutions have evolved to provide greater value across entire organizations, not just to a select few. And for data historians, it’s no different. Beyond traditional data analysts, a broader audience uses the systems. This democratization of data access is transforming how industrial organizations operate and make decisions.
While accurately collecting and archiving large volumes of real-time data remains crucial, industrial organizations now require more functionality due to the broadening user base. Modern data management solutions incorporate built-in visualization tools, dashboarding capabilities, and advanced analytics. This evolution has transformed data historians from time-series databases accessed by a select few into organization-wide comprehensive platforms for creating actionable insights. The data historian of today goes from a centralized location of raw data to a collaboration tool of data insights.
The current challenge of data historians then lies in providing the right information to the right people at the right time. As more individuals access these powerful data management tools, the data and insights presented must be relevant, actionable, and simplified – not overwhelming users with an ocean of raw data. The data must also be high quality and well managed – garbage in, garbage out applies. So, industrial data management must balance accuracy and completeness with ease of use to ensure industrial plants focus on the most critical aspects of their operations.
Centralizing Data as the Foundation for Smarter Operations
To ensure a balanced approach, industrial organizations should continually ask: “Why should we care about data management?” The answer goes beyond simply “because of data.” Data itself holds potential value, but it requires transformation to become meaningful and useful. Industrial data management solutions again should provide the right information to the right people at the right time, but there is no single definition of right.
With no single definition of right, data management solutions must be both scalable and flexible, capable of adapting to industrial users’ changing needs. With the ocean of data in industrial sites, organizations need a flexible data management framework and solution to handle diverse scenarios – from skimming the surface to diving into the depths, from navigating calm seas to riding out storms. Industrial data management must be versatile enough to:
- Address different levels of data complexity
- Serve various user roles across the organization
- Adapt to changing organizational priorities and market conditions
- Scale with growing data volumes and new data types
- Support both quick insights and deep, complex analyses
By focusing on these capabilities, industrial data management strategy not only handles current needs but also positions these organizations and environments for future growth and improvement. As a result, data management is foundational to industrial environments. It allows industrial organizations to extract maximum value from our data, turning potential into actionable insights that drive smarter operations and better decision-making across the entire organization. How an industrial organization manages, maintains, and uses its data will dictate its success now and in the future.